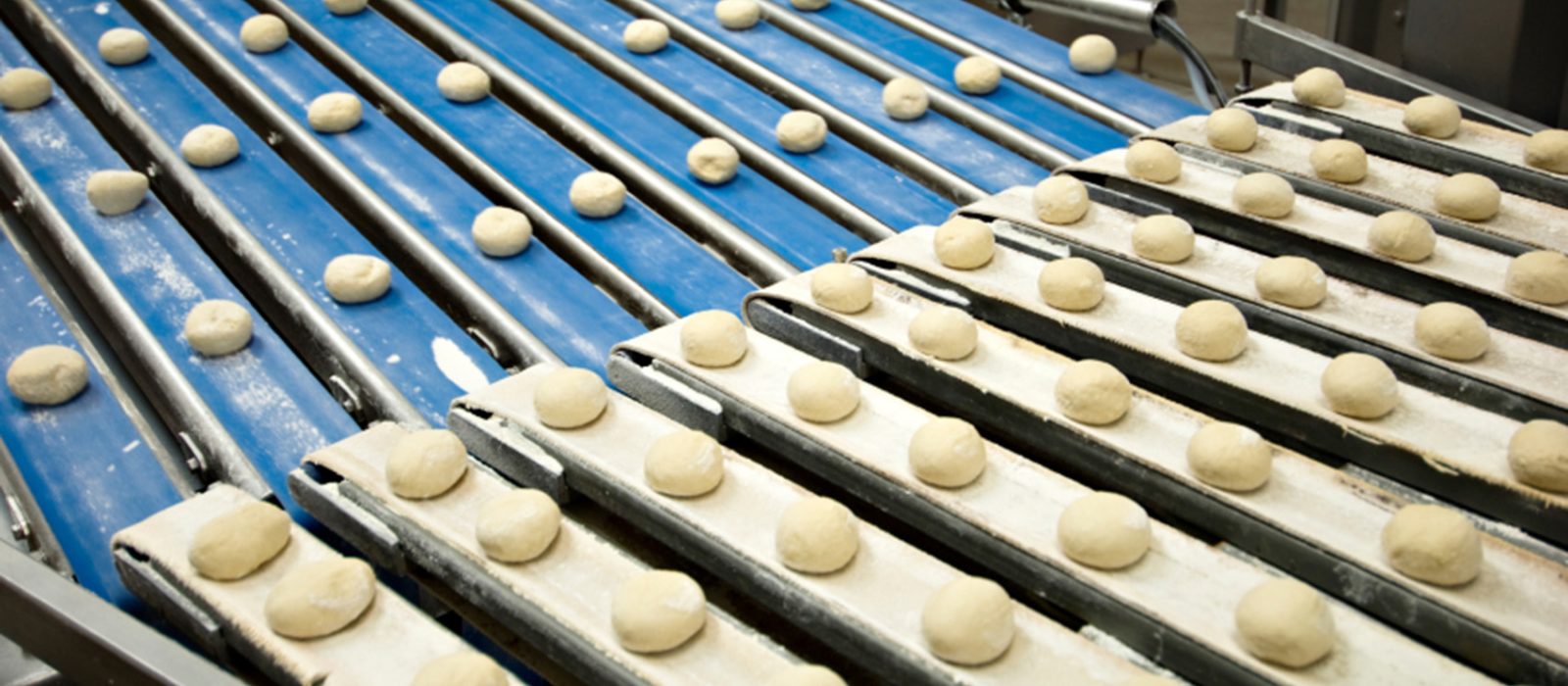
How to Properly Track A Bakery Conveyor Belt
Keeping a bakery running efficiently can be complicated. One of the most frequent challenges plant maintenance technicians have to deal with is conveyor belt tracking. Aligning and controlling a belt so it maintains its desired path is often difficult to do. So many factors influence the belt's ability to track correctly. Here are a few areas to consider when attempting to troubleshoot a mistracking conveyor belt.
1. Check for product, debris, and buildup
Most often the main source of mistracking is a result of product or basic materials built up on the bottom side of the conveyor belt or pulleys. Often this pending result can create a crown or raised portion on the pulley which can result in the conveyor belt mistracking to one side or the other. Inspecting a conveyor for mechanical and cleanliness issues needs to be a part of your standard preventive maintenance.
2. Check to ensure the conveyor frame is level and square
In the baking industry, product and line changes happen frequently. This usually means current conveyor systems are moved or modified to meet the latest production requirements. It is during this process a conveyor bed may become out of level or square. When a conveyor bed is out of level or square, the conveyor belt has a tendency to move toward one side or the other. This can be checked by utilizing a standard level. Be sure to check both the frame and the pulleys as well.
Making sure your conveyor bed is square is also easy to do. Simply measure the dimensions from one corner to the opposite corner on each side of the conveyor. The measurements should equal one another. Don’t worry if you’re slightly out of square, as most manufacturers provide what are referred to as squaring rods on the bottom side of the conveyor. These can be used to pull the frame back into alignment.
3. Check to ensure the end pulleys are square
Often the wrong pulley is used to track or adjust the belt. This is a common problem when the conveyor utilizes a center drive and tracking configuration. Start by checking to ensure every pulley is in proper alignment with the conveyor frame. Use only snub rollers and idlers to make tracking adjustments. If at all possible, avoid using the drive roller for tracking adjustment.
4. Check to ensure the conveyor belt has been cut straight
In the belt fabrication industry, we like to think all belts shipped are perfect, unfortunately, that is not always the case. When a belt is slit incorrectly, this can put an arc or curve into the belt, which will result in a mistracking condition. If the belt is not aligned correctly during the joining process (laced or made endless), this too can cause a mistracking condition. If you suspect this is the case, remove the conveyor belt from the conveyor, lay it out on a table or floor, and see if you notice an arc or curve in the belt. If it is not straight, the belt needs to be replaced.
Problem | Solution |
---|---|
Mechanical malfunction | Proper alignment of pulleys/ conveyor frame. |
Crooked splice | Square belt end, replace splice. |
Crooked belt | Replacement may be required, see crooked splice. |
Material build-up on pulleys | Recommend routine maintenance or mechanical cleaning devices. |
Off-center loading | Change feeder design or replace belt with more bulk. Add v-guide or tracking device. Check the belt manufacturer's technical specifications. |
Excessive pulley crown | Refer to CEMA (Conveyor Equipment Manufacturers Association) standard 402-1 964 or check with the technical specification of the belt manufacturer. |
Distorted belt because of runoff or accidental damage | Replacement of belt indicated. |
All Blog Posts