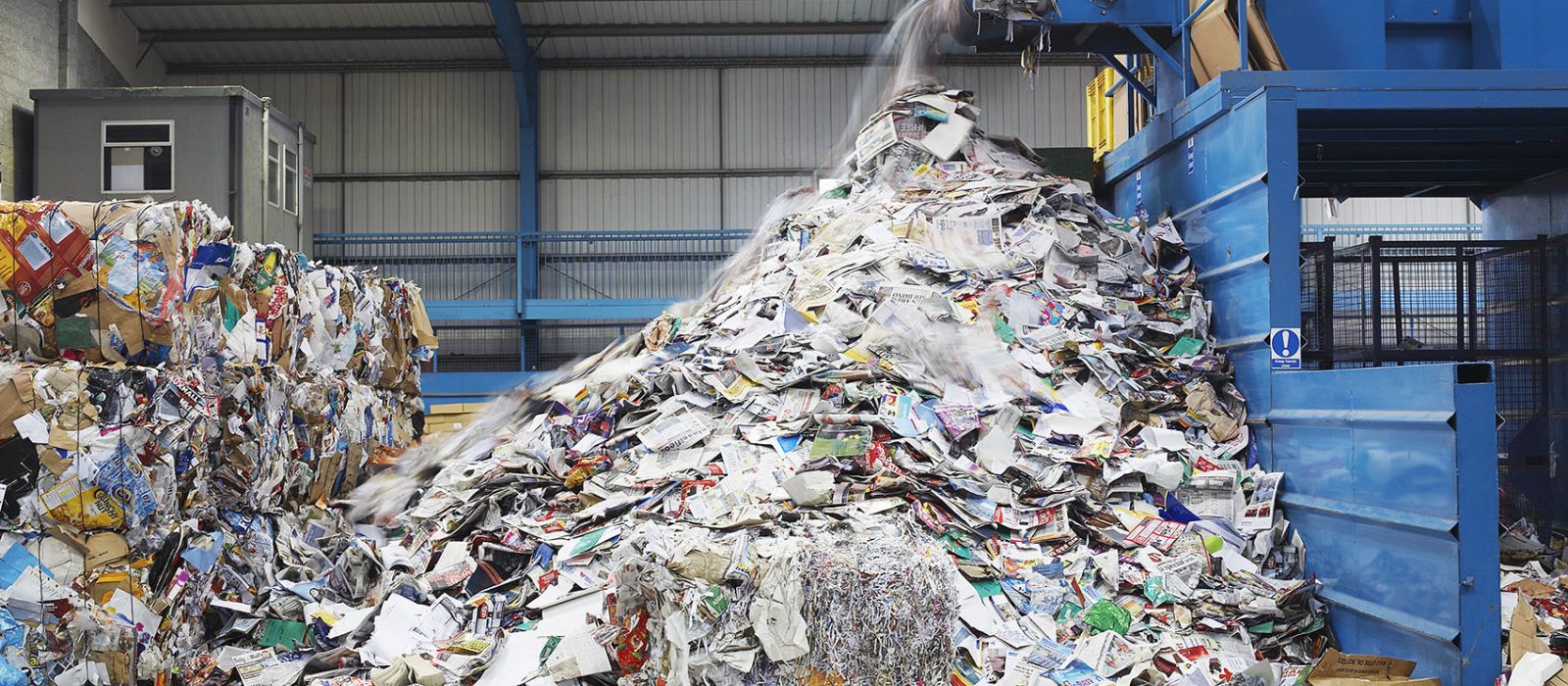
Belt Maintenance
The Ultimate Checklist: Common Causes of Conveyor Belt Tracking Issues
Aligning and controlling a belt so it maintains its desired path is often difficult to do. Many factors influence the belt's ability to track correctly.
Common Causes of Conveyor Belt Tracking Issues
- Pulleys, belts, or rollers contain material build-up
- Un-level foundation
- Damaged idler frames
- Improper belt storage which results in warping or bowing
- Excessive tensioning of the belt
- Pulleys out of alignment with the conveyor center line
- Self-aligning idlers installed incorrectly or need to be replaced
- Return idler spacing is too wide to track the belt
- Uneven or misaligned pulleys
- Uneven placement of load on the belt or the belt being loaded off center
- Uneven skirting pressure
- Worn pulley faces, pulley lagging unevenly worn, or pulley shaft locking elements worn
- Return idlers improperly installed resulting in the belt not making proper contact with rollers
- Offset trough idlers being used on reversing conveyors rather than in-line idlers being used
- Out of round or seized rollers giving the belt contact forces asymmetric to the center line
- Poor belt quality with the weave/fabric asymmetric to the center line
- Trough idlers installed back to front with the lead roller not leading
- Mechanical fasteners not installed square
- Conveyor rollers of various diameters installed
- Improper belt splicing
- Transition idlers not installed or unevenly adjusted
- Worn pulley faces
See our other posts for more information on properly tracking a conveyor belt:
- 4-step belt tracking process to properly align your belt
- How to properly track a bakery conveyor belt
- How to diagnose and fix common conveyor belt tracking issues
- Conveyor belt tracking tips
All Blog Posts
Contact a Sparks Representative For Help Tracking Your Conveyor Belt
Contact Us